About us
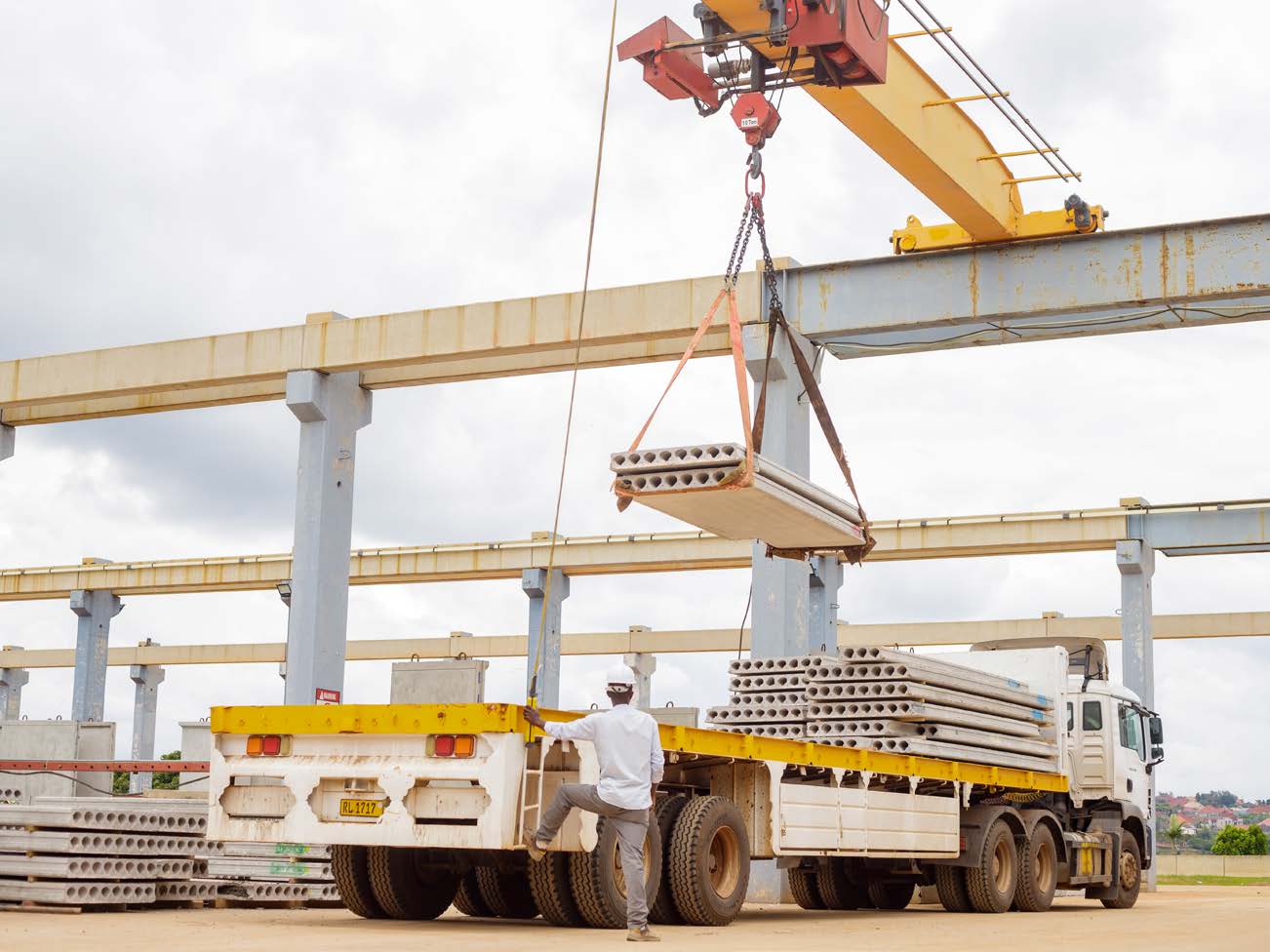
Recognized as one of the leading
AfriPrecast Ltd stands as Rwanda’s pioneering Precast Concrete Factory, established in December 2017 under the esteemed patronage of H.E Mr. Paul Kagame, the President of the Republic of Rwanda.
AfriPrecast Ltd has distinguished itself as a leading construction company in Rwanda, setting the standard for durability, innovation, and excellence in the industry by using precast material. Our success stems from the concerted efforts of highly organized and reliable teams comprising engineers, architects, designers, project managers, and professionals with diverse disciplines and extensive experience in the field.
- Quality is our hallmark. Every stage of our manufacturing process
- Our approach is innovative yet responsive. By deeply understanding market demands
- We gained the confidence of different Clients by providing best quality products
Our Story
Leveraging precast concrete technology, we aim to overcome high costs, skill shortages, and infrastructure deficiencies.
Since 2018, we’ve been in Rwanda, pioneering rapid building construction. Our focus on large-scale housing projects has resulted in successful, timely deliveries, addressing the market’s frustration with slow construction.
To ensure excellence, we’ve brought in international experts to complement our team of over 1000 Rwandans, with a significant number being women, across our various sites and factories.
Our approach is innovative yet responsive. By deeply understanding market demands, we tailor our designs to meet their specific needs, ensuring customer satisfaction.
Looking ahead, we aim to expand our operations to provide affordable housing, furthering our impact on Rwanda’s housing sector.
Quality is our hallmark. Every stage of our manufacturing process, conducted in controlled environments, upholds this commitment.
Affordable Housing Focus
AfriPrecast is dedicated to contributing to affordable housing initiatives in Rwanda. Our precast products, including hollow core slabs, wall panels, columns, and beams, are designed to streamline construction processes, reduce costs, and ensure durability, making them ideal for affordable housing projects.
Mission
Building a better sustainable world with innovative technologies.
Values
Vision
To be the recognized leader for innovative and transformative construction technology.
- Quality
- Innovative
- Customer Focus
- Integrity
- Safety
Our Production Process
Our production process goes through various stages from the time designs are made to the time you see an erect structure that adds value and elegance to your neighborhood. It all begins with receiving drawings from our in-house design department. These drawings undergo a thorough review by our skilled engineers to ensure all necessary materials are available.
Moulds, along with steel cages, are then fabricated. The cured elements are then transported to the site, where they are assembled during the various building stages until completion.
Next is the certification process. Once the quality control engineers certify them, casting takes place and this is followed with finishing the elements.
A material engineer checks the strength of the concrete before the elements are de- moulded and transported to the stockyard for curing.
The cured elements are then transported to the site, where they are assembled during the various building stages until completion. All elements in our factory are manufactured in a controlled environment under the strict supervision of our experienced and well-trained technical staff who closely monitor the production process of all elements from the design stage to erection. The production process is supervised at every step to ensure that our products get to the site when in perfect shape and of the highest quality.
Why choose AfriPrecast
- Labor-intensive with on-site formwork, scaffolding.
- Prolonged timelines, and higher risk of errors.
- Challenges in managing timelines & budgets.
- Delays and overruns from unforeseen issues.
- Prone to defects, rework, waste and reactive quality control.
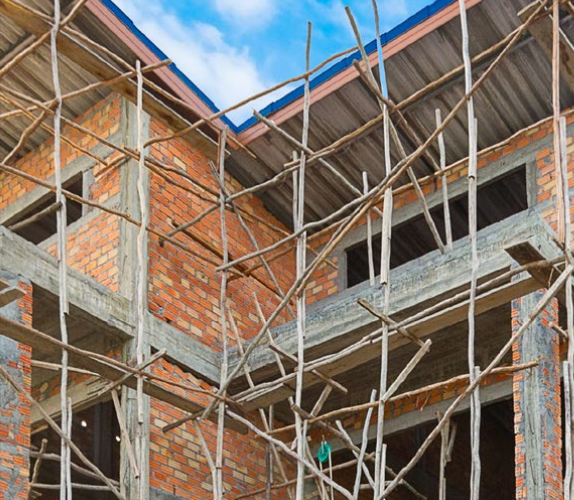
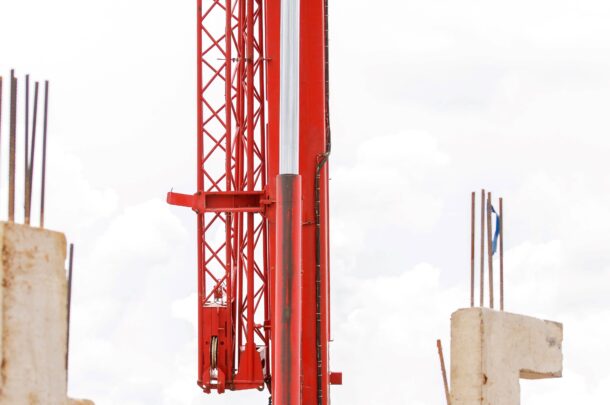
- High quality elements produced in well controlled environment.
- Cost effective.
- Speed execution works more than 50% reduction of construction compared to conventional construction.
- Swift installation without on-site formwork conventional construction.
- Weather friendly construction.
- Time saving installation.
- Excellent fire and sound resistance.
- Wear and tear resistance